Polycarbonate (PC) is formed into flat sheet by extrusion process. In the extrusion process, the polycarbonate is propelled continuous along a screw through region of high temperature and pressure where it is melted and compacted, and finally forced through a die shaped. PC can be extruded into different thickness:0.25mm,0.5mm,0.7mm, 0.8mm,1.0mm,1.2mm, 1.5mm and 2.0mm. Commonly used thickness is 0.5mm,0.7mm,0.8mm and 1.0mm.
PC can be mix with different colorant to get reflective, fluorescent, optical and transparent effect.
Screw extruder can be applied different texture to create texture PC sheet.
Coextrusion PC/PMMA. Films or sheets consist of layers of two or more different polymers can be produced by mixing the molten streams. This process can be used to combine materials to provide combination of properties that can not be obtained in a single polymer.
Vacuum forming PC can provide impact protection as skull protect brain.
Vacuum forming PC can be sliding layer to create MIPS function in order to manage rotational impact energy.
Thermoforming is a popular process for helmet manufacture, which putting a silkscreened color polycarbonate sheet into oven for preheat, placing the polycarbonate into vacuum machine, the sheet is heated to a pliable forming temperature, formed to a specific shape in a mold, different products shape and height would cause different stretching during vacuum forming, the thinner vacuum formed PC the more potential risk of color fadeaway or strength reduction of helmet, so it is critical to analyze and choose correct polycarbonate sheet thickness which relate to helmet quality and impacting test. and trimmed to create a usable product.
Before vacuum forming process, we apply a layer of protect film on the polycarbonate sheet after extrusion, the film protect Polycarbonate from scratching during EPS in-molding, and remove the protect film when final helmet assembly at the end.
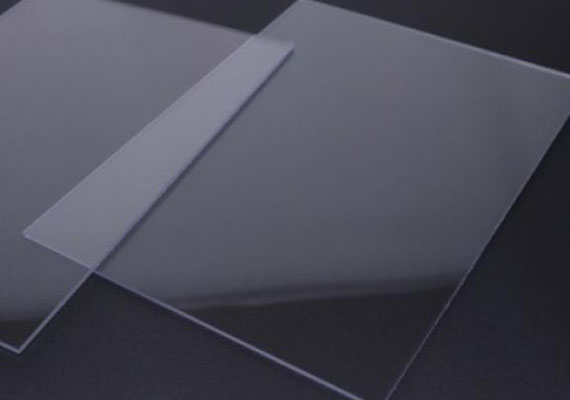
Composite PC PMMA
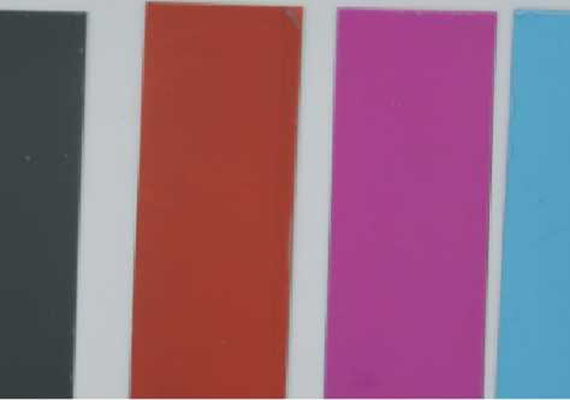
Transparent colorful PC
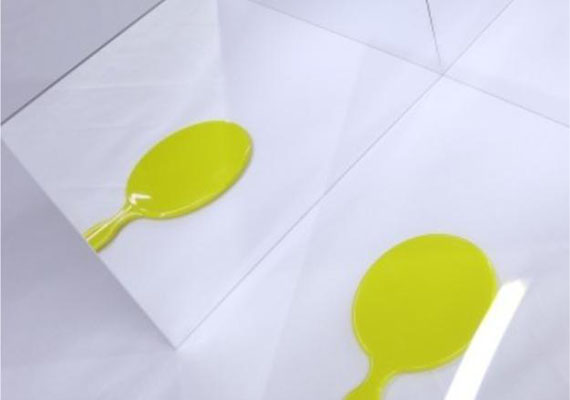
Mirror Optical PC
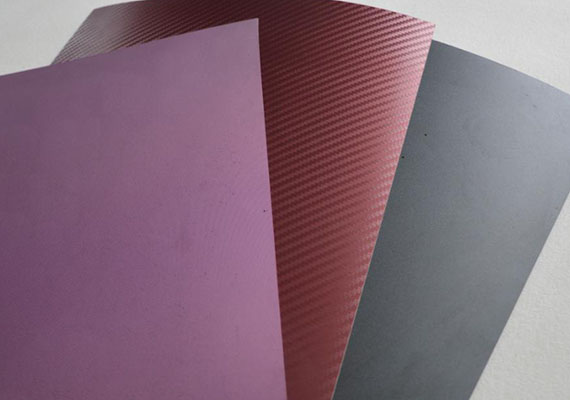
Textured PC
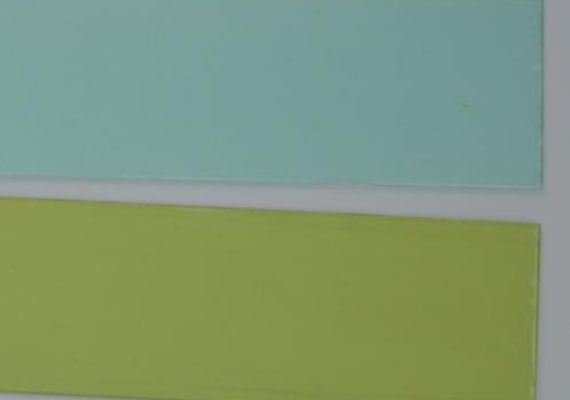
Fluorescent PC
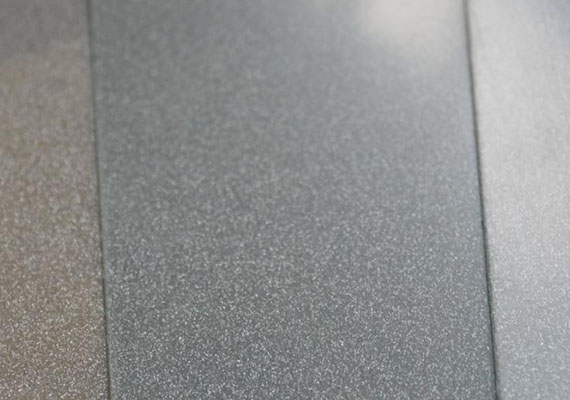